
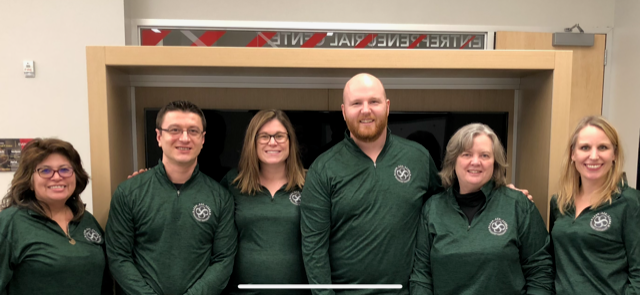
When Kathy Miner, Executive Director of Process Improvement at Davenport, talks about a fishbone diagram, it has nothing to do with marine biology or the culinary preparation of a catch of the day. Instead, she’s explaining a method for delving into complex problems.
“It’s a way of getting to root causes,” she explains. “You put the problem at the head and then branch out into all the things that could be impacting it — policies, people’s skill sets, procedures, and environmental influences like technology and the facility. When you’re done, it looks like the skeleton of a fish, but the diagram you’ve created is a thorough analysis of what’s really going on.”
Fishbone diagrams are just one of the tools and templates that Miner has introduced to Davenport during the past year as a part of the Lean Six Sigma pilot program. Developed decades ago in factories as a way to eliminate waste and reduce errors, Lean Six Sigma methods have since been successfully adopted in industries ranging from hospitals to wineries. Davenport is among the vanguard of universities now using these techniques to improve processes.
By definition, Lean Six Sigma is a fact-based, data-driven philosophy of improvement that values defect prevention over defect detention. It drives customer satisfaction and bottom-line results by reducing variation, waste and cycle time, while promoting the use of work standardization and flow. It has application anywhere there’s variation and waste, and can ultimately involve everyone in an organization.
The Pilot
Under executive sponsorship, five nominated employees participated in Davenport’s recently completed pilot program: Kelsey Daingerfield IPEx; Janet Maschke, Academic Information Systems; George Matache, Enrollment Operations; Vivianne Moore, College of Technology; and Dan Wait, Information Technology. The program is designed in a learn-practice-apply format with self-paced Six Sigma Green Belt Certification Curriculum modules, face-to-face classroom time, and applying the concepts and tools learned with assigned Lean Six Sigma Green Belt projects. Under the direction of Miner, who holds Black Belt certification, projects in the pilot included: Canceling a Class Process Improvement, Student Billing Process Improvement, and Closed Contact Guidelines Process Improvement. Each project team included a process owner plus staff from various functions who provided front-line expertise.
Overall, Miner and program participants felt the pilot was a successful experience. “I think the best thing about Lean Six Sigma is the getting organized – understanding what data is related to your processes and then which inputs are impacting your outputs in a less-than-desirable-way.
Year Two Now Underway
Building on the pilot’s success, Davenport’s Lean Six Sigma program officially launched on October 22 with 10 new participants from a variety of functions who delve into a new set of improvement opportunities once their Green Belt training is complete. Looking ahead, Miner envisions a cascading effect, with more employees participating every year and more processes improved by applying Lean Six Sigma techniques.
“The demand is growing,” she says. “People are calling me to ask about it and find out about future sessions. It’s been really an awesome experience to get Lean Six Sigma off the ground here.”
No Responses